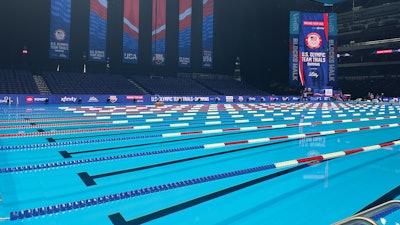
The world’s elite swimmers, divers and water polo players will vie for Olympic gold, silver and bronze beginning July 27 in Paris, but it’s a fourth type of metal that will hold the aquatics competitions together: stainless steel.
Nearly two dozen pools total have been erected out of stainless steel for the 2024 Summer Games, according to Mike Mintenko, director of sales at Myrtha Pools, which supplied the basins out of the company’s home base in Italy. Once all medals have been awarded, three of the pools — built specifically for swimming competitions and warmups — will be disassembled and repurposed in aquatic facilities elsewhere in France. The others will remain in place as more permanent legacies of the Paris Olympiad, the city’s first since 1924.
Photo courtesy of Myrtha
The portability afforded by Myrtha’s pool-building approach allows marquee swimming events to take place in virtually any venue. As recently as 2000, the U.S. Olympic Team Trials were held at the 4,700-seat Indiana University Natatorium in Indianapolis — marking the last U.S. Trials to be held in a permanent pool. In 2008, 2012, 2016 and 2020, the meet was held in Omaha, Neb., in an arena that held fewer than 20,000. For this year’s Trials, the sixth using Myrtha products, a stainless steel pool was sited where the Indianapolis Colts typically play NFL football — on the floor of 70,000-seat Lucas Oil Stadium.
“The reality is, in today’s world of competitive swimming, these championship events are seldomly done in permanent locations, because there’s not enough seating,” Mintenko says. “So, we bring the pool to the people instead of bringing the people to the pool.”
Photo courtesy of Myrtha
The Indy competition pool’s ultimate destination is 125 miles away in Fort Wayne, where it will be installed permanently for a second life that’s likely to span the next half-century or more, if the natatorium surrounding it holds up for that long. The vessel’s legacy as a Trials pool makes it easily marketable, according to Mintenko. “It’s an attraction to clients who want to purchase that pool,” he says, adding that it makes sense from Myrtha’s standpoint, too. “We don’t want to be storing pools. We’re not in that business. We’re in the business of putting pools in the ground. So, we discount the pools pretty heavily, and then we move them on, and another client builds them and starts the legacy of that pool in that new community. It’s a really neat opportunity, and that’s why I think a lot of people jump at it.”
Photo courtesy of RenoSys
Attractive alternative
Turns out, stainless steel offers multiple selling points for schools, municipalities and hospitality providers looking for an alternative to concrete-and-plaster pool construction. No pool-making material is as watertight for as long of a lifespan as stainless steel, but there are several means to achieve those ends.
Myrtha pools are put through a hot colander lamination process by which each individual steel panel is faced on its interior side with PVC, which bonds to the heated metal. “Imagine taking schedule 40 pipe and melting it onto the steel. That’s what the finish is like in the end,” Mintenko says.
Photo courtesy of RenoSys
The edges of each 3-foot-wide panel are then bent to form flanges on their exterior side, and those flanges are then fastened to flanges on each neighboring panel with bolts, nuts and washers. Panels are sized to varying heights — from less than 4 feet to 12 feet or more — depending on desired pool depths. “It’s all a giant, modular Erector Set that goes up quite quickly, and that’s why we do some of these temporary events,” Mintenko says. “Everything comes on pallets when it ships, and you can walk every piece through a standard-sized door.”
RenoSys and Natare Corporation, both manufacturers of permanent stainless steel pools, weld their panels together. Some welding will take place in climate-controlled conditions, and more welding will take place on the job site. “It’s a fully welded system, so there are no joints,” says RenoSys CEO Jason Mart. “It’s completely watertight.”
Photo courtesy of RenoSys
Natare goes so far as to preassemble sections of wall with a support structure and gutter system already attached. “We build those in shop, put them on a truck, ship them to wherever, and we’re placing those unitized sections 20 feet at a time. So, for a typical municipal pool, we’re not going to be on site very long,” says Troy Yoder, the company’s president and CEO, noting that panels can be laid out, secured to a concrete footer and welded together in a matter of weeks. “It kind of depends on the pool, but two to three weeks and you’re done. Compare that to the 30 days that a concrete pool needs to just sit and cure. That’s a big advantage right there.
“Once these panels are welded together, they’re going to be watertight and trouble-free. They’re not going to crack like a concrete pool would.”
Photo courtesy of Natare
Design delivered
Just how much piecing together takes place can vary pool to pool. “Depending on the size, we can do a single piece, weld it here in the shop, put it on a trailer, lift it up, put it in place,” Yoder says. “Or we can do it in sections. We recently shipped a pool to Salt Lake City that we built in-shop in four equal sections, and that pool in place is 22 feet wide by 75 feet long and 4 feet deep. Or we can do what we call stick-built. Say we’re building a pool in New Jersey, and access and logistics are a nightmare. Our stick-built pools are pre-engineered parts and pieces that fit on a typical 4-by-10-foot skid that would then fit in a freight elevator. You’re going to be able to manhandle that with just a pallet jack and get it close to where the pool is. And then our guys come in and weld together those pre-engineered pieces of the puzzle onsite. We’ll be longer onsite doing it that way, but sometimes that’s the only choice.”
Just how many pieces? “On a typical hotel pool that’s maybe 20 feet wide by 40 feet long, you’re going to have hundreds of pieces that are welded together,” Yoder says.
Photo courtesy of Natare
RenoSys delivers factory-welded pool corner assemblies to a job site along with 20-foot-wide wall sections. Thickness can range from 7 to 12 gauge, depending on the application, according to Mart, who is quick to point out that not all stainless steel is created equal. “The most important and most critical thing for consideration is what grade of stainless steel to employ,” says Mart, whose premium product — called Futura Pool — features a high-grade, low-carbon steel. “That’s one of the things that we take great pride in. It’s critical for rust resistance, and it’s especially important in high-salt areas. It’s considered marine-grade stainless steel, and that’s what we use with our 50-year warranty.”
When asked if a concrete pool can possibly compete with that kind of longevity, Mart says, “It depends on where it’s built, more than anything else. If a pool is built in Wisconsin, that would be a long life. Your pool might still be useful, but you’d be doing several renovations.”
Photo courtesy of Natare
Welded pools also offer a PVC lining option, typically lightly adhered to the steel wall once welding is completed in the field and further held in place by water pressure as the pool is filled. Linings serve several purposes. They protect the steel from corrosion, rust and degradation of welded joints — “It’s called stainless, not stainnotatall,” Mart says — but it also allows for concrete floors to complement the steel walls as a cost-saving measure. Moreover, stainless steel doesn’t accept paint particularly well, so PVC membranes also allow for the demarcation of lane lines in competition pools, while lending pools their widely accepted (and expected) blue color.
That is not to say that a pool can’t be stainless steel top to bottom, with the bottom perhaps treated for slip resistance. “We have lots of stainless pools that are bare stainless, and they look beautiful,” Yoder says. “Others have PVC membrane just on the bottom. Others have membrane on the floor and the walls. And ceramic tile is also an option. Budget plays a factor in which finish you want, and it kind of goes in that order. Bare stainless would be most affordable, and then the membrane and then ceramic tile.”
All stainless steel pools, whether backfilled in the ground or freestanding in a temporary above-grade setting, are supported by a buttress system made of either stainless steel (often in elevated applications such as rooftop pools) or coated carbon steel (inground). “That gets bolted down to the concrete footer, and then those pool sections are welded together,” Mart says.
Stainless steel also allows all manufacturers the ability to bend pools into just about any shape imaginable. “It’s fully customizable,” says Yoder, pointing to the Marriott Marquis Houston hotel, which features a sixth-floor lazy river in the shape of Texas. “That is 100 percent stainless steel, with all the curves and corners.”
Locally sourced stainless steel can significantly impact a pool’s final price tag. While welding is more expensive than bolting, Mart says completed RenoSys pools are more affordable than the rival stainless variety and competitively priced with concrete. “We are dealing directly with communities, so we don’t have multiple layers of markup,” he says. “It’s all U.S.-manufactured stainless.”
Myrtha uses U.S. steel if specified by an American client, but that steel will first have to make a round trip to Italy and back. That’s a rare occurrence, however, and overall business is booming. France has emerged as one of Myrtha’s top markets, according to Mintenko, who estimates 400 stainless steel pools have been installed there over the past 20 years. That’s still roughly half the number of Myrtha pools that have popped up in the states since 2000, when the company opened an office in Sarasota, Fla. One luxury apartment project in Miami, the 60-story Porsche Design Tower, features more than 100 pools alone.
“We get involved in a lot of really cool projects, for sure,” Mintenko says. “But our bread and butter is always going to be our competition and municipal recreation projects.”
The Hulbert Aquatic Center in West Fargo, N.D., boasts a record board with times Michael Phelps — holder of a record 28 Olympic medals — once swam when the Hulbert pool first served the U.S. Olympic Team Trials. Not every facility can leverage that kind of legacy — as of this summer, a dozen Trials pools had been transitioned into community aquatics assets — but perhaps the greatest bragging rights of any stainless steel pool take the form of longevity and low maintenance. An initial investment that’s higher than that of concrete will no doubt pay dividends in terms of decades-long peace of mind.
“Yes, stainless steel is more expensive than mud. It just is. It’s a higher-level product, and it does cost more,” Mintenko says. “The real value is in not having to go back and replaster, repaint, retile — the inherent maintenance that you have with traditional construction. If you did a concrete pool, and you had to go back every seven years or 10 years or 12 years, that’s time when that concrete pool is shut down. It’s not being operated, patrons aren’t using it, and the community is not getting the benefit of that facility.
“There are still many, many pools in the U.S. that are shotcrete/gunite-type pools with a plaster finish, and I think that’s always going to be the case. But I do see a lot of clients coming from scenarios where they have built those pools, those pools have lived their useful life, and the clients are changing the choice of technology to stainless steel for a different product and, in many of their cases, a different outcome — a much, much more durable pool for the life of the entire facility.”