Recycled (and recyclable) pavers are gaining traction as a green alternative to concrete.
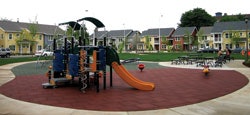
There are those who believe a big eraser should be taken to the USGBC's LEED guidelines with regard to building materials touting their recycled content. Yes, products such as recycled rubber surfaces keep tires out of landfills, goes this argument, but what is the hidden environmental cost of producing these materials?
One longtime critic, the unnamed LEED-certified sustainability expert who authors sincerelysustainable.com (a blog that seeks "true sustainability in the marketplace"), put it this way: "First of all, these products' embodied energy is usually very high due to the energy-intensive processes involved in combining often dissimilar materials and getting the recycled materials back into a usable form. Secondly, composite material-based products often fail to surpass, or at best match, the durability, ease of use and aesthetics of their more commonly used, and often less expensive, 'non-green' counterparts . . . It can often be argued that such composite material-based products are not only 'non-green,' but also don't qualify as a superior, or even satisfactory, replacement for the applicable product for which they were designed to replace."
Those remarks actually appeared in a rave review last year of a recycled rubber paver, both because of the manufacturer's efforts and because the material the pavers replace, concrete, "sucks for the environment." (Concrete involves one of the world's most energy intensive manufacturing processes, the author wrote, and is responsible for almost a tenth of the CO2 released into the atmosphere annually.) Indeed, recycled-content pavers are one of the most common products exhibited at the annual GreenBuild conference, and have made huge inroads in outdoor commercial settings in parks and playgrounds, around pools and as pathways. The products not only keep tires and plastic bottles out of landfills, they ease the "heat island" effect of concrete while providing greater resilience.
Rubber pavers have achieved their greatest notoriety as replacements for concrete sidewalks. Their inventor, Richard Valeriano, the senior public works inspector in Santa Monica, Calif., worked with U.S. Rubber Recycling Co. in the late 1990s on a prototype after noting the amount of money spent by municipalities on pruning tree roots and repairing concrete walkways buckled by roots. A 2001 incident in Gardena, Calif. - in which a local screenwriter, Lindsay Smith, convinced Los Angeles County to temporarily halt the removal of dozens of trees while she looked for an alternative - led to the further development of Valeriano's invention, saved some of Smith's neighborhood flora and created what was to become Rubbersidewalks Inc., Smith's second career.
Slip resistant and shock absorbent, recycled rubber pavers are now formulated to more closely resemble concrete in their appearance and hardness. An early concern was that pedestrians might be tripped up by the change in surface rebound as they walked from concrete to rubber or back again, but published reports suggest that cities installing rubber sidewalks have had fewer slip-fall lawsuits because of their greater resilience and the disappearance of cracked and buckled concrete. The only lingering question remains their life-cycle cost - no one knows how long rubber pavers will hold up to the elements, although advances in outdoor tracks suggests that this should be of little concern.
Rubbersidewalks says that one square foot of its product recycles waste rubber from one passenger tire, and that each 20-square-foot installation saves one tree from removal. But the best news of all? Recycled rubber pavers can themselves be recycled and reused at the end of their lifespan.