The dog days of August mean different things to different people - family vacations, football practices, back-to-school sales.
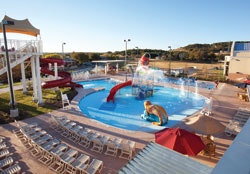
The dog days of August mean different things to different people - family vacations, football practices, back-to-school sales. For many facility operators, it's the winding down of the outdoor pool season and, soon after, the beginning of the pool construction season.
Shovels often go into the ground immediately after Labor Day, because this gives the owner the best chance of having a new pool ready to greet swimmers on Memorial Day. Whether the timetable will be maintained depends on a host of factors, the most variable of which is weather. Yet, there is nothing strange about pool construction commencing at a time when (to cite a prominent example) road construction crews are working overtime to finish up before the first freeze. The fact is that, except in extreme conditions, pool construction can proceed as long as precautionary measures are taken by the owner, aquatics consultant and pool contractor.
Scheduling pool construction, whether indoors or out, will nearly always be affected by seasonal changes in weather. An average outdoor aquatic facility with a lap pool and a small leisure pool typically takes six to nine months to construct, with those located in colder climates on the longer end of the spectrum because of weather delays. For indoor pools, the pool basins can be constructed before or after the construction of the natatorium structure around it, but it is more typical for the basins to be prepared first, with building contractors taking care not to damage the pool shell during construction. (When pools are constructed after the natatorium is built, the pool contractor needs to make sure the pool shell construction does not undermine the building foundations.)
Aside from weather and the desired timing of project completion, scheduling is also affected by the scope and location of the project, construction funding and project permitting. Although demolition or excavation can be done at any time of year, it is certainly easier prior to the arrival of winter, so a great deal of preparation is necessary to achieve even the day-after-Labor-Day groundbreaking. Assuming construction begins as planned, excavation and pool shell construction take place in the fall, along with the shell of the bathhouse. The pool's mechanical equipment and other bathhouse fixtures are then installed during the winter and, when spring arrives, pool finishes, the pool deck and landscaping are completed so that the pool can open on time for the summer swim season.
In cases where a later, less favorable start date is selected (or where the schedule has been pushed back significantly), facility owners should become familiar with the following aspects of cold-weather pool construction:
Concrete Placement. The two most common methods of concrete placement for pools are cast-in-place concrete or pneumatically applied concrete (shotcrete). In cold weather (which American Concrete Institute Section 306 specifications define as "a period when for more than three consecutive days the mean daily temperature drops below 40°F"), keep an eye on the pool contractor and make sure measures are taken to shield the concrete for the duration of the placement and curing stages. Things to look for are blankets, portable heaters, windbreaks, enclosures and insulated forms. These precautionary measures are not needed once the ambient temperature climbs above 50°F for at least 12 hours.
Typically, concrete gains compressive strength at a slower rate at lower temperatures than it does at higher temperatures. The temperature effect on concrete's compressive strength gain can be partially offset by using high early strength cement as opposed to normal type cement (that is, Type III instead of Type I). Another cold-weather concrete placement option to discuss with your pool contractor involves air-entrainment (in which tiny air bubbles are intentionally created in the concrete). Entrained air is beneficial for concrete placed during freezing weather because air entrainment supplies capacity within the concrete to absorb stress forces resulting from ice accumulation.
Water Tightness Test. Even during cold weather, the new concrete pool shell should be tested for water tightness prior to the application of the pool finish. The concrete structure should set for 28 days for curing purposes and to gain sufficient strength to withstand the water loading. After all the inlets and main drains have been securely sealed, and the forecasted temperatures are above 40°F for the next three days, the pool shell can be filled with water, allowing the concrete shell to absorb water. The water used for this test must be within 10°F of the concrete pool shell temperature to avoid concrete cracking. After three days, the concrete will have absorbed as much water as it can, and the water tightness test can begin.
Pool Finishes. Each of the four most common types of pool finishes has different temperature requirements:
- Epoxy Paint - The surface to which the paint is applied should have a minimum temperature of 35°F and be at least 5°F above the dew-point temperature, as it will not cure if the temperature is lower.
- Marcite Plaster - All materials and affected areas should remain above 50°F for 24 hours prior to and 72 hours after placement of the pool plaster. If applied in cold weather, the plaster coat may separate and create a hollow space between the plaster coat and the concrete pool wall. This development usually occurs after a few years and is likely accelerated by freeze/thaw cycles.
- Quartz Aggregate Plaster - As with marcite plaster, all materials and affected areas should remain above 50°F for 24 hours prior to and 72 hours after placement.
- Tile - Normal tile installation conditions are considered to be 73°F and 50 percent relative humidity. Typically, colder temperatures and higher humidity will require longer cure times. There are special tile bonding products that can be used in temperatures as low as 40°F; these products come at a premium cost, but they reduce the cure time and limit the time required to protect the installation from submersion and freezing.
Familiarizing yourself with some basic information about cold-weather pool construction will allow you to intelligently discuss the project with all parties through the construction process, helping above all to ensure that your contractor is taking the proper precautions. Ultimately, though, facility owners need to be aware that the project's successful completion on schedule during cold weather will depend to a large extent on weather severity through the fall and winter.